
The 2nd International Electronic Conference on Actuator Technology
Part of the International Electronic Conference on Actuator Technology series
4–6 November 2024
Compact Actuator System, Medical Transducer, Drone, Actuator for Crisis Technology, Energy Harvesting System, Autonomous Actuator
- Go to the Sessions
- Event Details
-
- Welcome from the Chairs
- Program Overview
- IECAT 2024 Program (DAY 1)
- IECAT 2024 Program (DAY 2)
- IECAT 2024 Program (DAY 3)
- Live Session Recordings
- Poster Gallery
- Abstract Book
- Event Chairs
- Event Speakers
- Sessions
- Registration
- Instructions for Authors
- Publication Opportunities
- List of Accepted Submissions
- Event Awards
- Sponsors and Partners
- Conference Secretariat
- Events in series IECAT
Conference Closed-Thank You for Your Participation!
The Best Oral Presentation Awards and Best Poster Award of IECAT2024 have been announced. Please pay attention to Event Awards updates for detailed information and winner announcements.
Participants of this conference are cordially invited to contribute a full manuscript to our Special Issue "Actuator Technologies and Control: Materials, Devices and Applications", in Actuators (ISSN: 2076-0825, Impact Factor: 2.2), with a 20% discount on the publication fee. Full details can be found here.
Welcome from the Chairs
Dear Colleagues,
You are cordially invited to participate in the 2nd International Electronic Conference on Actuator Technology (IECAT), sponsored by MDPI’s open access journal Actuators. The meeting is an opportunity for researchers in the field of actuator engineering and technology to present their research and exchange ideas with colleagues. This is a virtual conference via Zoom.
This Second Conference will focus on “Sustainability and Crisis Technologies”, in addition to general topics in accordance with the aims and scope of the journal Actuators.
- New actuator materials - Piezoelectrics, Magnetostrictors, Shape memory alloys; Elastomer actuators
- Innovative actuator designs - Ultrasonic motor; MEMS/NEMS
- New actuators for control systems, Intelligent control, Fault and attack-tolerant control, Power supply, Switching regulator, AC/DC converter
- Remarkable actuator applications - Biomedical actuators, Robotics, Crisis technologies, Aerials, Surface and underwater vehicles; Energy harvesting
Your submitted paper will be reviewed and published in a Special Issue of the journal Actuators with a discount of 20% on the article processing charge (ISSN 2076-0825; Actuators).
We look forward to engaging in exciting discussions and hearing new ideas and perspectives from experts in the actuator field. All participants are welcome to join the online conference.
Kind regards,
Prof. Kenji Uchino, MS, MBA, Ph.D.
The Pennsylvania State University
Follow the conference organizer on Social Media
Program Overview
4th November - Afternoon | 5th November - Afternoon | 6th November - Afternoon |
Session 1. New actuator materials | Session 2. Innovative actuator designs | Session 3. Drive/control technologies Session 4. Remarkable actuator applications |
IECAT 2024 Program (DAY 1)
IECAT 2024 Day 1
Session 1. New actuator materials
Date: 4th November 2024 (Monday)
Time: 13:00 (CET, Basel) | 7:00 (EDT, New York) | 21:00 (JST, Tokyo)
Time in CET | Speakers | Title |
13:00-13:10 | Prof. Dr. Kenji Uchino Event chair |
Welcome from the Event Chair |
13:10-13:50 | Prof. Dr. Kenji Uchino Event chair |
Piezoelectric Actuator – History “From Discovery to Commercialization” |
13:50-14:20 | Dr. Aslan Miriyev Session chair |
Soft Actuation in the Era of Physical AI |
14:20-14:50 | Dr. Weimin Huang Keynote Speaker |
Laminated Composites with High Tan Delta over Wide Temperature Range |
14:50-15:20 | Dr. Brittany Newell Invited Speaker |
Additively Manufactured Actuators |
15:20-15:35 | Ouriel Bliah | Digital light processing 3D printing of stretchable and compressible porous polymers for soft robotics |
IECAT 2024 Program (DAY 2)
IECAT 2024 Day 2
Session 2. Innovative actuator designs
Date: 5th November 2024 (Tuesday)
Time: 13:00 (CET, Basel) | 7:00 (EDT, New York) | 21:00 (JST, Tokyo)
Time in CET |
Speakers | Title |
13:00-13:10 | Prof. Dr. José Luis Sánchez-Rojas Session chair |
Welcome from the Session Chair |
13:10-13:40 | Prof. Victor Ruiz Invited speaker |
Hybrid 3D-printed and MEMS Sensors and Actuators |
13:40-14:10 |
Dr. Manmatha Mahato |
Structural Carbon Materials for Electrochemical Soft Actuators |
14:10-14:25 | Víctor Corsino | Advanced AI-Integrated Sensor Systems for Liquid Monitoring: From 3D-Printed Resonators to Piezoelectric MEMS actuators |
14:25-14:40 | Daniel Calegaro | A piezo-actuated on-chip testing device for the micromechanical characterization of the SiO2-polysilicon interface |
IECAT 2024 Program (DAY 3)
IECAT 2024 Day 3
Session 3. Drive/control technologies
Date: 6th November 2024 (Wednesday)
Time: 14:00 (CET, Basel) | 8:00 (EDT, New York) | 22:00 (JST, Tokyo)
Time in CET |
Speakers | Title |
14:00-14:10 | Prof. Dr. Paolo Mercorelli Session chair |
Welcome from the Session Chair |
14:10-14:40 | Prof. Dr. Satoshi Ueno Invited speaker |
Principle and analysis of a five-axis active suspended axial-gap self-bearing PM motor |
14:40-15:10 |
Prof. Dr. Dong Jiang |
Advanced Pulse Width Modulation and Motor Drives |
15:10-15:40 | Prof. Dr. Paolo Mercorelli Keynote Speaker |
Some Control Strategies for MagLev Actuators |
15:40-15:55 | Uros Ilic | The electromagnetic vibratory actuator load during the transport of a rigid body on a vibratory conveyor |
15:55-16:10 | Damian Tamburi | Advanced control strategies based on reinforcement learning for linear actuators |
16:10-16:25 | Farid Yousef | Colibri: Hovering Flight of a Robotic Hummingbird |
Session 4. Remarkable actuator applications
Date: 6th November 2024 (Wednesday)
Time: 16:25 (CET, Basel) | 10:25 (EDT, New York) | 00:25 (JPT, Tokyo)
Time in CET |
Speakers | Title |
16:25-16:55 | Prof. Dr. Norman M. Wereley Session chair |
Additive Manufacturing in Magnetorheological Systems: MR Elastomers, Encapsulants and Cellular Materials |
16:55-17:10 | Ved Prakash Dubey | Controlled Deployment of Polymeric Composite Hinges for Space Applications |
17:10-17:25 |
Carl Johan Gøbel Nielsen |
Adaptive Deployable Polymer Reflector for CubeSats |
17:25-17:40 | Maxim Wischnewski | A Multilayer Piezoelectric Thermo-Magnetic Film Generator |
17:40-17:55 | Abhiram Gunaratnam | An electric linear actuator-based lysimeter soil retriever design: Performance optimization and performance loss measurement |
17:55-18:10 | Ziyue Piao | Assessing the Impact of Force Feedback in Musical Knobs on Performance and User Experience |
Live Session Recordings
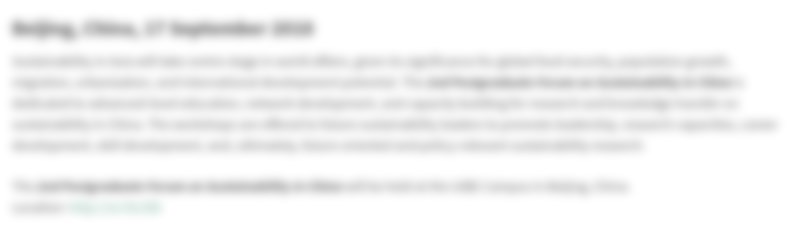
Abstract Book
The online version of the Conference Abstracts Book including all abstracts, is available to browse and download!
Event Chairs

Kenji Uchino, one of the pioneers in piezoelectric actuators, is Academy Professor at Emeritus Academy Institute, The Pennsylvania State University. He was Director of International Center for Actuators and Transducers, Materials Research Institute, and Professor of EE and MatSE, Distinguished Honors Faculty of Schreyer Honors College at The Penn State University. He was also the Founder and Senior Vice President & CTO of Micromechatronics Inc., State College, PA from 2004 till 2010, then, Associate Director at The US Office of Naval Research – Global Tokyo Office (US Ambassador to Japan) from 2010 till 2014. Uchino is Life Fellow in both IEEE and Americal Ceramic Society. Keywords: piezoelectric materials, device designing, precision positioners, micro-robotics, ultrasonic motors, smart structures, piezoelectric transformers, energy harvesting.

Université Libre de Bruxelles, Belgium

Institute of Microstructure Technology, Karlsruhe Institute of Technology (KIT), Germany
Session Chairs

Prof. Dr. José Luis Sánchez-Rojas
Microsystems, Actuators and Sensors Lab, INAMOL-Universidad de Castilla-La Mancha, Spain
MEMS/NEMS; piezoelectric microsystems; integrated sensors and transducers; miniaturization of instrumentation for applications in chemistry; food technology; robotics; biotechnology and IoT

Prof. Dr. Kenji Uchino
Academy Professor, Emeritus Academy Institute, The Pennsylvania State University, University Park, USA
piezoelectric actuator; ultrasonic motor; piezo-transformer; high power piezoelectrics; loss mechanism; Pb-free piezoelectrics; piezoelectric composite; multilayer actuator; relaxor piezoelectric single crystal; piezoelectric energy harvesting; piezoelectric driver

Prof. Zongli Lin
Charles L. Brown Department of Electrical and Computer Engineering, University of Virginia, USA
nonlinear systems; nonlinear control; constrained control; systems with time delays; active magnetic bearings

Dr. Aslan Miriyev
Physical AI (PAI) Laboratory, Department of Mechanical Engineering, Ben-Gurion University of the Negev, Israel
physical AI (PAI); material intelligence; soft-material robotics; bio-hybrid robotics; soft actuation; bio-hybrid actuation; soft and structural functional composites; multi-material systems; advanced manufacturing; 3D printing

Prof. Dr. Norman M. Wereley
Department of Aerospace Engineering, University of Maryland, USA
smart materials and structures; actuators; sensors; dampers; energy absorbers; pneumatic artificial muscles; control systems; applications to aircraft, ground vehicles, and robotic system

Prof. Dr. Gary M. Bone
Department of Mechanical Engineering, McMaster University, Canada
robot design, sensing and control; collaborative robots (Cobots); 3D machine vision for robots; robot learning from demonstration; soft pneumatic actuators; hybrid pneumatic-electric actuators; advanced control algorithms for pneumatic and hybrid actuator

Prof. Dr. Paolo Mercorelli
Institute for Production Technology and Systems (IPTS), Leuphana Universität Lüneburg, Germany
control systems; mechatronics; actuators; engines control; signal processing; wavelets; Kalman filter; optimal energy control

Prof. Dr. Dong Jiang
Huazhong University of Science and Technology, Hubei, China
power electronics; motor drives
Event Committee

Department of Industrial Engineering, University of Florence, Italy
smart materials; stimuli-responsive materials; bioprinting; tissue engineering; biomaterials

State Key Lab of Mechanics and Control of Mechanical Structures, Nanjing University of Aeronautics and Astronautics, China
piezoelectric actuators; ultrasonic motors; nano fabrications; ultrasonic sensors; micro/nano manipulations

Department of Industrial and Manufacturing Engineering, High Performance Materials Institute, Florida State University, USA
printed electronics; Composites for Electronics and Optics (CEO); Additive Thin-film Manufacturing (ATM)

Department of Advanced Science and Technology, Faculty of Engineering, Toyota Technological Institute, Japan
piezoelectric actuator; piezoelectric mover; control of piezoelectric actuator; driver for piezoelectric actuator; near-field ultrasonic levitation; vibration-assisted machining

Department of Aerospace Engineering, University of Maryland,College Park, USA
smart materials and structures; actuators; sensors; dampers; energy absorbers; pneumatic artificial muscles; control systems; applications to aircraft, ground vehicles, and robotic system

actuation for aerospace (servo-hydraulic, electro-hydrostatic, electromechanical); architecting; system level modelling and simulation; control; testing; virtual validation

lignin-derived resins; nanocellulose multifunctional composites; smart materials and devices, including electroactive polymers; power harvesting; soft actuators; biosensors; flexible electronics; smart optics

School of Mechanical and Aerospace Engineering, Nanyang Technological University, Singapore
shape memory materials and technology; sensors and actuators; 4D printing

Laboratory of Image Signal and Intelligent Systems, Department of Network & Telecom, University of Paris-Est Créteil, France
wearable robotics; physical human robot interaction; robotics

Institute of Mechatronics, Kaunas University of Technology, Lithuania
adaptive piezomechanical systems, smart materials, structures and devices, microsystems dynamics, biomechanics/biomechatronics, robotics, energy harvester, real-time data analysis and control, etc.

Department of Industrial Engineering, University of Naples “Federico II”, Italy
thermo-fluid dynamic stability; flow control; synthetic jet actuators; free surface flows

State Key Laboratory of Rail Transit Vehicle System, Southwest Jiaotong University, China
magnetic levitation theory and application; electromagnetic field computation; high temperature superconductors

School of Engineering, College of Engineering and Physical Sciences, University of Birmingham, UK
soft robotics; pneumatic muscles; end effectors; automation for food; healthcare robotics

Institute for Production Technology and Systems (IPTS), Leuphana Universität Lüneburg, Germany
control systems; mechatronics; actuators; engines control; signal processing; wavelets; Kalman filter; optimal energy control

School of Mechanical, Materials, Mechatronic and Biomedical Engineering, University of Wollongong, Australia
motion control; robotics and biomectronics

Systems Department, National Institute for Aerospace Research “Elie Carafoli” – INCAS, Romania
mechanohydraulic, electrohydraulic, and electromechanical actuators; active and semi-active control; antiblocking systems (ABS); smart aerospace structures; structural health monitoring (SHM); stability robustness and performance robustness

Department of Systems Engineering and Department of Material Science and Engineering, Saarland University, Germany
smart material systems; actuators; sensors; dielectric elastomers; shape memory alloys; elastocalorics

Department of Mechanical Engineering, McMaster University, Hamilton, Canada
robot design, sensing and control; collaborative robots (Cobots); 3D machine vision for robots; robot learning from demonstration; soft pneumatic actuators; hybrid pneumatic-electric actuators; advanced control algorithms for pneumatic and hybrid actuator

Department of Structural Engineering, University of California San Diego, USA
stimuli-responsive materials; nanocomposites; sensors and actuators; soft materials; tomography

Department of Mechanical Engineering, Saitama University, Japan
mechatronics; magnetic bearing; magnetic suspension; vibration control; force and mass measurement; micro assembly

Department of Mechanical Engineering, University of Michigan, USA
Structural dynamics and controls, including the emerging areas of intelligent structural & material systems harnessing origami dynamics, reconfigurable metamaterials/metastructures, and mechano-intelligence, with applications in vibration & noise controls
Keynote Speaker

School of Mechanical and Aerospace Engineering, Nanyang Technological University, Singapore
Laminated composites for deployable hinges
Invited Speakers

Department of Mechanical engineering, Korea Advanced Institute of Science and Technology (KAIST)
Structural Carbon Materials for Electrochemical Soft Actuators

Purdue University Polytechnic Institute School of Engineering Technology Adaptive Additive Technologies Lab, USA
Additively Manufactured Actuators

Department of Mechanical Engineering, College of Science and Engineering, Ritsumeikan University, Kusatsu, Japan
Principle and analysis of a five-axis active suspended axial-gap self-bearing PM motor

Hybrid 3D-printed and MEMS Sensors and Actuators
Registration
Registration for IECAT 2024 will be free of charge! The registration includes attendance at all conference sessions.
If you are registering several people under the same registration, please do not use the same email address for each person, but their individual university email addresses. Thank you for your understanding.
Please note that the submission and registration are two separate parts. Only scholars who registered can receive a link to access the conference live streaming. The deadline for registration is 31 October 2024.
Instructions for Authors

Deadline for abstract submission: 7 July 2024 11 August 2024
Deadline for abstract acceptance notification: 7 August 2024 8 September 2024
Announcement of oral and poster abstract results: 26 August 2024 23 September 2024; You will be notified of the acceptance of an oral/poster presentation in a separate email.
Abstract Submission
1. Abstract submissions should be completed online by registering with www.sciforum.net and using the "New Submission" function once logged into the system. No physical submission is necessary.
2. The abstract should include an introduction, methods, results, and conclusion sections, and be within 600 words in length (1 figure/table is a Standard Format. No figure/table or 2 figures/tables may be also accepted.).
3. All accepted abstracts will be published in the conference report of IECAT2024 in MDPI’s Proceedings journal (ISSN: 2504-3900) after quality check. If you wish to publish a research article in the journal, please refer to the “Publication Opportunities” Section.
4. All abstracts should be submitted and presented in clear, publication-ready English with accurate grammar and spelling.
5. You may submit multiple abstracts. However, only one abstract will be selected for oral presentation.
6. All abstracts accepted for presentation will be collected in a book of abstracts, which will be published on the website after the conference.
7. The abstracts submitted to this conference must be original and novel, without prior publication in any journals or it will not be accepted to this conference.
1. The submitting author must ensure that all co-authors are aware of the contents of the abstract.
2. Please select only one presenter for each submission. If you would like to change the presenter after submission, please email us accordingly.
Note: We only accept live presentations.
The slot for the oral presentation is 15 minutes. We recommend a 12-minute presentation, leaving about 3 minutes for a Q&A session.
Authors are encouraged to prepare a presentation in PowerPoint or similar software, to be displayed online along with the abstract. Slides, if available, will be displayed directly on the website using the proprietary slide viewer at Sciforum.net. Slides can be prepared in exactly the same way as for any traditional conference where research results are presented. Slides should be converted to PDF format prior to submission so that they can be converted for online display.
Poster Presentation
a. Your submission should include the title, authors, contact details, and main research findings, as well as tables, figures, and graphs where necessary.
b. File format: PDF (.pdf).
c. Size in cm: 60 width x 80 height–portrait orientation.
d. Font size: ≥20.
e. Maximum size: 250 M
You can use our free template to create your poster. The poster template can be downloaded here.
Authors who wish to present a poster are invited to send it to the conference email at iecat2024@mdpi.com. All posters will be permanently exhibited online in the Poster Gallery.
It is the authors' responsibility to identify and declare any personal circumstances or interests that may be perceived as inappropriately influencing the representation or interpretation of clinical research. If there is no conflict, please state "The authors declare no conflicts of interest." This should be conveyed in a separate "Conflict of Interest" statement preceding the "Acknowledgments" and "References" sections at the end of the manuscript. Any financial support for the study must be fully disclosed in the "Acknowledgments" section.
MDPI, the publisher of the Sciforum.net platform, is an open access publisher. We believe authors should retain the copyright to their scholarly works. Hence, by submitting an abstract to this conference, you retain the copyright to the work, but you grant MDPI the non-exclusive right to publish this abstract online on the Sciforum.net platform. This means you can easily submit your full paper (with the abstract) to any scientific journal at a later stage and transfer the copyright to its publisher if required.
Publication Opportunities
Participants in this conference are cordially invited to contribute a research article to the Special Issue "Actuator Technologies and Control: Materials, Devices and Applications", published in Actuators (ISSN: 2076-0825, Impact Factor: 2.2), with a 20% discount on the publication fee. Please note if you have IOAP/association discounts, conference discounts will be combined with IOAP/association discounts. Conference discounts cannot be combined with reviewer vouchers. All submitted papers will undergo MDPI’s standard peer-review procedure. The abstracts should be cited and noted on the first page of the paper.
List of accepted submissions (25)
Id | Title | Authors | |||||||||||||||||||||||||||||||||||||||
---|---|---|---|---|---|---|---|---|---|---|---|---|---|---|---|---|---|---|---|---|---|---|---|---|---|---|---|---|---|---|---|---|---|---|---|---|---|---|---|---|---|
sciforum-108637 | Drone trajectory tracking control: A comparative study of PID, Sliding mode, and Backstepping controllers enhanced by Gray Wolf Optimization. |
Show Abstract |
|||||||||||||||||||||||||||||||||||||||
Unmanned Aerial Vehicles (UAVs) are transforming various fields, from surveillance to agriculture, necessitating advanced control systems for effective operation. This study explores three prominent control strategies for UAV trajectory tracking: Proportional-Integral-Derivative (PID) control, Sliding Mode Control (SMC), and Backstepping Control. Each method is enhanced through Gray Wolf Optimization (GWO), a nature-inspired algorithm designed to determine the optimal control gains, thereby maximizing performance in real-world scenarios. The paper begins by providing a thorough overview of each control technique, elucidating their underlying principles and typical applications in UAV systems. We employ GWO to fine-tune the parameters of each controller, enabling a systematic approach to optimization that takes advantage of the algorithm's ability to converge towards global optima. This optimization is critical, as the success of UAV operations heavily relies on precise trajectory tracking, which is inherently influenced by the selected control strategy. To evaluate the effectiveness of each approach, we conduct a series of simulations that track the UAV’s performance across various trajectories. Key performance indicators such as speed, precision, and robustness are meticulously analyzed. The results illustrate significant variances in how each controller performs under different operational conditions, with a detailed discussion of their respective advantages and limitations. For instance, while the PID controller is noted for its simplicity and ease of implementation, it may struggle with robustness in dynamic environments. In contrast, the Sliding Mode Controller exhibits superior resilience to disturbances, yet may require more complex tuning. The Backstepping Control method, on the other hand, demonstrates exceptional precision, particularly in complex maneuvers, but can be computationally intensive. This comparative analysis provides crucial insights for researchers and practitioners in the UAV domain, highlighting the importance of selecting the appropriate control strategy based on mission requirements. By integrating GWO into the optimization process, we pave the way for more efficient and reliable UAV control systems, ultimately contributing to the advancement of autonomous aerial operations. The findings underscore the potential for future work to explore hybrid control approaches that leverage the strengths of each method, further enhancing UAV capabilities in increasingly complex environments. |
|||||||||||||||||||||||||||||||||||||||||
sciforum-108431 | Modeling and Performance Optimization of a Lithium Niobate-Based Pyroelectric Sensor Using Finite Element Analysis | , |
Show Abstract |
||||||||||||||||||||||||||||||||||||||
This study presents a detailed analysis of a pyroelectric detector based on a lithium niobate (LiNbO₃) crystal for optimizing its performance under different geometrical configurations and electrical load conditions. The effect of varying the pyroelectric disk radius and thickness, as well as the electrical load resistance, on voltage, current, power, and temperature profiles, was thoroughly investigated. Results indicate that larger disk radii (up to 5 mm) enhance voltage and current sensitivity, thereby maximizing power output. However, larger radii also lead to slower temperature decay, highlighting the need for efficient thermal management to prevent structural overheating and maintain long-term functionality. Additionally, increasing the disk thickness from 0.01 mm to 0.04 mm results in substantial improvements in voltage, current, and power, with the most significant changes occurring between 0.01 mm and 0.02 mm. Conversely, thicker disks show better heat dissipation, helping mitigate temperature rise. The analysis of varied electrical load resistances reveals that lower resistances (1 kΩ) generate higher power and voltage outputs, while higher resistances reduce the system’s electrical response. These findings underscore the importance of optimizing both geometrical and electrical parameters to enhance the overall performance and thermal stability of pyroelectric detectors in practical applications. These findings provide valuable insights for optimizing pyroelectric sensor performance through geometric and electrical load adjustments. Future work includes the fabrication of the sensor using the optimized parameters, followed by experimental validation to assess its real-world performance. |
|||||||||||||||||||||||||||||||||||||||||
sciforum-108279 | Advanced AI-Integrated Sensor Systems for Liquid Monitoring: From 3D-Printed Resonators to Piezoelectric MEMS actuators | , , |
Show Abstract |
||||||||||||||||||||||||||||||||||||||
Abstract - In modern industry, the integration of sensors with advanced artificial intelligence (AI) algorithms is essential for enhancing workflow efficiency and decision-making capabilities. This work introduces two innovative approaches that use these technologies to monitor and analyze liquid properties in real-time, shown in Figure 1. In the first approach (Figure 1 (a)), we designed a cuboid-shaped fluidic cell [1], fabricated from various materials using novel 3D printing techniques, featuring a vibrating membrane at its base with two external piezoelectric actuators attached. The second approach (Figure 1 (b)) employed micromachined plates driven by AlN piezoelectric films, fabricated using MEMS technology, meticulously designed to achieve quasi-free-free vibration in the (0,5) mode [2]. Both types of sensors used a two-port structure, one for actuation and the other for detection. The integration of these devices with AI techniques allowed us to use frequency responses in a range with multiple resonances, highly sensitive to fluid properties [3], while eliminating the need for complex electronics to process and acquire data. Figure 1. (a) Top and cross-sectional views of the 3D-printed liquid cell with piezoelectric actuators. (b) Portable, low-cost viscometer-densimeter that included a MEMS microresonator, a microcontroller unit, and conditioning electronic circuits. The system incorporated a 3D-printed fluidic cell for injecting liquid into the sensor. The spectra obtained with the sensors were subjected to various advanced data processing and machine learning techniques, performing an exhaustive search for the optimal combinations of hyperparameters that best fit the sensor data. Convolutional neural networks (CNNs) were found to be highly effective in working with frequency characteristics and estimating the viscosity and density of different types of liquids. In the second approach, these models were implemented on a microcontroller board, which also managed all electronics and communication with the sensor, resulting in a precise, compact, portable, and low-cost device. Cell-based systems proved effective for monitoring the properties of aqueous solutions, achieving calibration errors below 2% and resolutions of 7.79 · 10-3 mPa·s for viscosity, and 1.09 · 10-3 g/mL for density. The microelectromechanical resonator-based instrument was capable to detect very small adulterations in olive oil with other vegetable oils, as low as 2%, with calibration and resolution errors of 0.47% and 0.14 mPa·s for viscosity, and 0.0331% and 9.25 · 10-5 g/mL for density. The calibration and resolution accuracies obtained were comparable to or exceeded those in the state of the art, and were on par with other commercial laboratory instruments of greater complexity, cost, and stationary nature. Our findings demonstrate the significant potential of integrating sensors with machine learning techniques to achieve accurate detection of physical properties in fluids and address complex and critical industrial challenges, such as olive oil fraud. These advancements pave the way for the development of next-generation sensors that are not only accurate and reliable but also scalable and adaptable to diverse applications, providing valuable tools for the new industry. |
|||||||||||||||||||||||||||||||||||||||||
sciforum-108206 | Elevating mobile robot performance: Metaheuristic optimization of PID control for linear speed and angular position |
Show Abstract |
|||||||||||||||||||||||||||||||||||||||
This article presents a comprehensive study on the control of linear speed and angular position in mobile robots using Proportional-Integral-Derivative (PID) controllers, with a focus on optimizing PID gains through metaheuristic optimization techniques. We begin by developing a detailed mathematical model of the robotic system, capturing its dynamics and response characteristics. Utilizing metaheuristic algorithms, such as Genetic Algorithms and Particle Swarm Optimization, we adaptively tune the PID parameters to enhance system performance in varying operational environments. The simulation results demonstrate significant improvements in trajectory tracking accuracy, reduced overshoot, and quicker settling times compared to conventional PID approaches. Additionally, the optimized PID controller showcases robust performance under different conditions, validating the effectiveness of our modeling and optimization strategy. This research not only highlights the potential of metaheuristic methods in fine-tuning PID controllers but also provides valuable insights into the simulation of mobile robotic systems, contributing to advancements in robotic control and navigation technologies. |
|||||||||||||||||||||||||||||||||||||||||
sciforum-106211 | Optimizing solar efficiency: MPPT control using PSO metaheuristics under partial shading constraint |
,
,
Ayoub Raji ,
|
Show Abstract |
||||||||||||||||||||||||||||||||||||||
In photovoltaic (PV) systems, efficient energy extraction is critical, especially under partial shading conditions where multiple local maxima can complicate the search for the true Maximum Power Point (MPP). This paper presents a robust approach to Maximum Power Point Tracking (MPPT) using the Particle Swarm Optimization (PSO) metaheuristic, tailored specifically for partial shading scenarios. The PSO method is advantageous due to its ability to handle the complex, non-linear nature of the power-voltage (P-V) and current-voltage (I-V) characteristics under varying irradiance levels. Unlike conventional MPPT techniques, which may converge to local maxima, the PSO-based method dynamically adjusts the duty cycle of the DC-DC converter, efficiently navigating the search space to locate the global MPP. The proposed method is evaluated through extensive simulations, where it consistently demonstrates superior performance in tracking the true MPP, regardless of the shading pattern. The paper provides a detailed analysis of the P-V and I-V curves under different shading conditions, showcasing how the PSO algorithm outperforms traditional methods in both convergence speed and accuracy. The results indicate a significant improvement in the power output of the PV system, highlighting the effectiveness of PSO in optimizing energy harvest. This study contributes to the growing field of renewable energy by offering a reliable and efficient solution for maximizing power generation in partially shaded PV systems. |
Event Awards
On behalf of the chairs of IECAT 2024 Conference, we are pleased to announce the winners of the Best Oral Presentation Awards and Best Poster Award.
The Best Oral Presentation Awards have been awarded to
Sciforum-099989 |
Ouriel Bliah, Seonggun Joe, Roei Reinberg, Lucia Beccai, Shlomo Magdassi | Digital light processing 3D printing of stretchable and compressible porous polymers for soft robotics |
sciforum-108279 | Victor Corsino, Víctor Ruiz-Díez, José Luis Sánchez-Rojas | Advanced AI-Integrated Sensor Systems for Liquid Monitoring: From 3D-Printed Resonators to Piezoelectric MEMS actuators |
sciforum-099139 | Farid Yousef, Han Wang, Wang Liang, Preumont André |
Colibri: Hovering Flight of a Robotic Hummingbird |
sciforum-100141 | Carl Johan Gøbel Nielsen, André Preumont | Adaptive Deployable Polymer Reflector for CubeSats |
sciforum-104623 | Ziyue Piao, Christian Frisson, Bavo Van Kerrebroeck, Marcelo Wanderley | Assessing the Impact of Force Feedback in Musical Knobs on Performance and User Experience |
The Best Poster Award have been awarded to
Sciforum-104731 | Tomoya Fujino; Daisuke Yamaguchi; Takefumi Kanda; Shuichi Wakimoto | Prototype of film endoscope for narrow environment using textured film actuator and small camera |
The Awards
Number of Awards Available: 6
The Best Oral Presentation Award is given to the submission judged to make the most significant oral contribution to the conference.
The Best Poster Award is given to the submission judged to make the most significant and interesting poster for the conference.
The winner will receive a certificate and 200 CHF each.
Sponsors and Partners
For information regarding sponsorship and exhibition opportunities, please click here.
Organizers
Media Partners
Conference Secretariat
Ms. Camille Li
Ms. Alethea Liu
Ms. Katrina Zhang
For inquiries regarding submissions and sponsorship opportunities, please feel free to contact us.
Email: iecat2024@mdpi.com
S1. New actuator materials
- Piezoelectrics, magnetostriction, shape memory alloy, elastomer actuator materials;
- MEMS/NEMS.
-
High-power density actuator materials;
-
Energy-harvesting materials and compositions, multi-ferroic materials (i.e., mechano-electric, magneto-electric, and thermo-electric materials);
-
Crystallographic orientation dependence of actuator performances;
-
Power MEMS, thick film fabrication, MEMS micro-machining;
-
Materials and suitable actuator designs.
Session Chairs
Prof. Dr. Kenji Uchino, Academy Professor, Emeritus Academy Institute, The Pennsylvania State University, University Park, USA
Dr. Aslan Miriyev, Physical AI (PAI) Laboratory, Department of Mechanical Engineering, Ben-Gurion University of the Negev, Israel
Show all published submissions (2) Hide published submissions (2)
Submissions
List of Papers (2) Toggle list
S2. Innovative actuator designs
Ultrasonic motor, MEMS/NEMS
Modelling and simulation of actuator systems from packaged systems down to device level and CAD tools. Electrostatic, piezoelectric, mechanical, thermal, acoustic, magnetic or any physical actuation principles. Miniaturization and low power. Micro- and nano-electromechanical systems (MEMS/NEMS). Ultrasonic motors and nano-positioning systems. Optical MEMS (MOEMS) and optoelectronic actuators. Chemical and bioactuators, and artificial muscles. Hybrid sensors and actuators. Calibration, characterization, and testing techniques for actuator devices. Reliability, failure analysis, degradation mechanisms, and lifetime prediction. System integration design strategies, interface electronics, packaging and assembly, 3D integration techniques, and mechatronics models.
Session Chair
Prof. Dr. José Luis Sánchez-Rojas, Microsystems, Actuators and Sensors Lab, INAMOL-Universidad de Castilla-La Mancha, Spain
Show all published submissions (7) Hide published submissions (7)
Submissions
List of Papers (7) Toggle list
S3. Drive/control technologies
Session Chairs
Prof. Dr. Zongli Lin, Charles L. Brown Department of Electrical and Computer Engineering, University of Virginia, USA
Prof. Dr. Paolo Mercorelli, Institute for Production Technology and Systems (IPTS), Leuphana Universität Lüneburg, Lüneburg, Germany
Prof. Dr. Dong Jiang, Huazhong University of Science and Technology, Hubei, China
Show all published submissions (7) Hide published submissions (7)
Submissions
List of Papers (7) Toggle list
S4. Remarkable actuator applications
Session Chairs
Prof. Dr. Norman M. Wereley, Department of Aerospace Engineering, University of Maryland, USA
Prof. Dr. Gary M. Bone, Department of Mechanical Engineering, McMaster University, Hamilton, Canada
Show all published submissions (9) Hide published submissions (9)
Submissions
List of Papers (9) Toggle list