
Applied Sciences Webinar | Challenges and Opportunities for the Design and Development of Human-Centric Systems Towards Industry 5.0
Part of the Applied Sciences Webinar series
8 March 2022, 15:00 (CET)
Human centric systems, Human Technology Integration, Social Sustainability, Smart Manufacturing, Industry 5 0, Operator 5 0, Society 5 0
Welcome from the Chair
3rd Webinar of Applied Sciences
Challenges and Opportunities for the Design and Development of Human-Centric Systems Towards Industry 5.0
Manufacturing and Production Industries are currently being reshaped in an attempt to integrate the new Information and Communication Technologies (ICT) in the existing workplaces. This shift has been encapsulated by several initiatives around the world, most commonly known as the "Industry 4.0". Manufacturing and Production systems can be connected, and most importantly can interact with virtual environments, by analyzing data and making decisions based on complex numerical simulation models. However, since the European Commission released its Industry 5.0 Policy in 2021, several research efforts focused on the comparison of Industry 4.0, Industry 5.0 and Society 5.0 as well. The comparison extends to the validity of Industry 5.0. The ongoing Fourth Industrial Revolution is technology-focused. On the other hand, Industry 5.0 (or Society 5.0 with Japanese perspective) is a more value-driven approach, towards the implementation of the available enabling technologies in industry. This new model is based on three interconnected core pillars as follows: human-centricity, sustainability, and resilience. Additionally, in Industry 5.0, the human-centric approach emphasizes that people have the right to decide what happens to them disregarding the fear of coercion or compulsion. It can be convincingly argued that the data generated about humans (including the social existence and the community as a whole) is inextricably linked to the lived personhood of any and every human being in the digital age. As a result, new "digital human/operator rights" are surfacing, and the human-centric paradigm is built on them. As such, Human-Centricity is a new way of thinking about data management and its possibilities in terms of data generation in manufacturing and focuses on key terms such as (self)sovereignty, self-determination, self-governance, autonomy, agency and so on. Therefore, the importance of Industry 5.0 should be further highlighted. In this context, the contribution of this presentation is focused on the transition from Industry 4.0 to Industry 5.0 taking into account the key technologies that can be used to enhance the abilities of the new generation of human operators, also known as Operator 5.0.
Date: 8 March 2022
Time: 3:00 pm CET丨9:00 am EST丨10:00 pm CST Asia
Webinar ID: 899 0630 9675
Webinar Secretariat: applsci.webinar@mdpi.com
Chair

Laboratory for Manufacturing Systems and Automation, Department of Mechanical Engineering and Aeronautics, University of Patras, Rio Patras, Greece
Manufacturing and production industries are currently undergoing transformations in order to integrate new information and communication technologies (ICT) into existing workplaces. European Commission released its Industry 5.0 Policy in 2021 and since then several research efforts have focused on the comparison of Industry 4.0, Industry 5.0, and Society 5.0. On the one hand, Industry 4.0 is technology-driven. Industry 5.0, on the other hand, is a value-driven approach towards the implementation of the available enabling technologies in industry. Human-centricity, sustainability, and resilience are the three interconnected core pillars of this new model. Furthermore, the human-centric approach in Industry 5.0 emphasizes that people have the right to choose what happens to them without fear of coercion or compulsion and new "digital human/operator rights" have emerged. As a result, the significance of Industry 5.0 should be emphasized. The contribution of this presentation is focused on the transition from Industry 4.0 to Industry 5.0, considering the key technologies that can be used to improve the abilities of the new generation of human operators, also known as Operator 5.0.
Professor in the Department of Mechanical Engineering and Aeronautics, Vice President of Research and Development of the University of Patras, Governing Board Member of the University of Patras at the Clean Aviation Joint Undertaking, and Founding Member of the Teaching Factory Competence Center. His research interests are focused on Manufacturing Systems, Robotic Systems, Automation Virtual and Augmented Reality in Manufacturing and Manufacturing Processes Modelling and Energy Efficiency. He is a Fellow Member of the International Academy for Production Research (CIRP), of the International Federation of Automatic Control (IFAC), of the International Federation of Information Processing (IFIP), of the Presidential Board of the International Association of Learning Factories (IALF), of the American Society of Mechanical Engineers (ASME) and of the Society of Manufacturing Engineers (SME) among others. He has published more than two hundred and ninety scientific papers and the unique citations of his published work exceed 9.400 (h-index 49).
Invited Speakers

Department of Industrial Engineering, Tecnológico de Monterrey, Mexico
The Resilient Operator 5.0" reinforces the human-centric and social sustainability characteristics of "The Operator 4.0” and adds — resilience — to the quest of designing and developing better human and human-machine systems that combine the unique capabilities of humans and machines towards smarter and more resilient manufacturing systems. This presentation aims to provide a vision for the future of work in the emerging Industry 5.0 hallmark and suggests how to use Industry 4.0 technologies to achieve socially sustainable working environments without compromising production objectives.
Prof. Dr. David Romero is a Professor of Advanced Manufacturing at the Tecnológico de Monterrey, Mexico. His research interests include: Circular Manufacturing, Service Engineering and Product-Service Systems, Cyber-Physical Systems & Human Systems, Advanced Production Management Systems, and Digital Lean Manufacturing. He has published +100 articles and serves at different academic, industry and government boards and committees in the disciplines of business and industrial engineering supporting digital transformation. He is recognized as the father and driving force of the Operator 4.0 / Operator 5.0 vision focused on promoting a socially sustainable Industry 4.0 and upcoming Industry 5.0.

Department Chair of Mechanical and Aerospace Engineering, Case Western Reserve University, Cleveland, OH, USA
As the fundamental building blocks of Industry 4.0, artificial intelligence plays a critical role in advancing the state-of-manufacturing. The ability in extracting clues from sensing data to guide the action of assistive infrastructure such as robots is essential to enhancing process control and production planning. This seminar highlights research on machine learning for human-robot collaborative assembly, where machine learning methods for the recognition of current actions and prediction of future actions of human operators during assembly operations are highlighted. This provides prerequisites for human-robot collaborative assembly and the potential of use-inspired basic research in advancing the state of manufacturing.
Dr. Robert Gao is the Cady Staley Professor of Engineering and Department Chair of Mechanical and Aerospace Engineering at Case Western Reserve University in Cleveland, Ohio. Since receiving his Ph.D. degree from the Technical University of Berlin, Germany in 1991, he has been working-signal transduction methods, stochastic modeling, and machine learning for improving the observability of dynamic systems such as manufacturing equipment and processes, with the goal to improve process- and product- quality control. Prof. Gao is a Fellow of the IEEE, ASME, SME, and CIRP (International Academy for Production Engineering). He has published more than 400 technical papers, including more than 180 journal articles, three books, and holds 13 patents. He is a recipient of the SME Eli Whitney Productivity Award, ASME Blackall Machine Tool and Gage Award, IEEE Instrumentation and Measurement Society’s Technical Award, IEEE Best Application in Instrumental and Measurement Award, and a CAREER award from the US National Science Foundation. He is a Senior Editor for the IEEE/ASME Transactions on Mechatronics.
Webinar Content
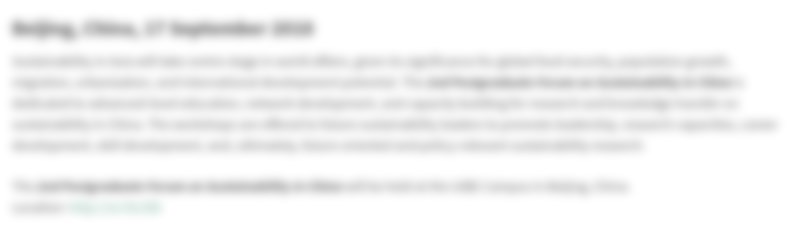
Program
Speaker & Presentation |
Time (CET) |
Prof. Dr. Dimitris Mourtzis Chair Introduction |
3:00 – 3:10 pm |
Prof. Dr. Dimitris Mourtzis Industry 5.0: Towards Human-Centric Manufacturing Short Abstract Manufacturing and production industries are currently undergoing transformations in order to integrate new information and communication technologies (ICT) into existing workplaces. European Commission released its Industry 5.0 Policy in 2021 and since then several research efforts have focused on the comparison of Industry 4.0, Industry 5.0, and Society 5.0. On the one hand, Industry 4.0 is technology-driven. Industry 5.0, on the other hand, is a value-driven approach towards the implementation of the available enabling technologies in industry. Human-centricity, sustainability, and resilience are the three interconnected core pillars of this new model. Furthermore, the human-centric approach in Industry 5.0 emphasizes that people have the right to choose what happens to them without fear of coercion or compulsion and new "digital human/operator rights" have emerged. As a result, the significance of Industry 5.0 should be emphasized. The contribution of this presentation is focused on the transition from Industry 4.0 to Industry 5.0, considering the key technologies that can be used to improve the abilities of the new generation of human operators, also known as Operator 5.0. |
3:10 – 3:30 pm |
Q&A |
3:30 – 3:35 pm |
Prof. Dr. David Romero Towards the Resilient Operator 5.0 Short Abstract The Resilient Operator 5.0" reinforces the human-centric and social sustainability characteristics of "The Operator 4.0” and adds — resilience — to the quest of designing and developing better human and human-machine systems that combine the unique capabilities of humans and machines towards smarter and more resilient manufacturing systems. This presentation aims to provide a vision for the future of work in the emerging Industry 5.0 hallmark and suggests how to use Industry 4.0 technologies to achieve socially sustainable working environments without compromising production objectives. |
3:35 – 4:00 pm |
Prof. Dr. Robert Gao AI-Enhanced Human-Robot Collaborative Assembly Short Abstract As the fundamental building blocks of Industry 4.0, artificial intelligence plays a critical role in advancing the state-of-manufacturing. The ability in extracting clues from sensing data to guide the action of assistive infrastructure such as robots is essential to enhancing process control and production planning. This seminar highlights research on machine learning for human-robot collaborative assembly, where machine learning methods for the recognition of current actions and prediction of future actions of human operators during assembly operations are highlighted. This provides prerequisites for human-robot collaborative assembly and the potential of use-inspired basic research in advancing the state of manufacturing. |
4:00 – 4:25 pm |
Q&A |
4:25 – 4:35 pm |
Discussion and Concluding Remarks |
4:35 – 5:00 pm |
Attendees are welcome to type in their questions in the Zoom Q&A section!
Relevant SI
Intelligent, Sustainable and Resilient Personalized Product-Service Systems towards Industry 5.0
Guest Editors: Prof. Dr. Dimitris Mourtzis, Prof. Dr. Carmen Constantinescu & Prof. Dr. Nikolaos Papakostas
Deadline for manuscript submissions: 30 April 2022