
The 2nd International Electronic Conference on Machines and Applications
Part of the International Electronic Conference on Machines and Applications series
18–20 June 2024
Automation and control, Electrical Machines, Turbomachinery, Intelligent Machines, Additive Manufacturing, Condition Monitoring, fault diagnosis
- Go to the Sessions
- Event Details
-
- Winner Announcement
- Welcome from the Chair
- Event Chairs
- Event Speakers
- Program Overview
- IECMA 2024 Program (DAY 1)
- IECMA 2024 Program (DAY 2)
- Abstract Book
- Poster Gallery
- Live Session Recordings
- Sessions
- Registration
- Instructions for Authors
- Publication Opportunities
- List of Accepted Submissions
- Event Awards
- Sponsors and Partners
- Conference Secretariat
- Events in series IECMA
The IECMA 2024 is closed! Thanks for your participation!
Welcome to submit your paper to the conference's special issue of Machines with 20% discount!
Deadline: 15 February 2025.
Submit your proceeding paper (4-8 pages) to Engineering Proceedings journal for free!
Deadline: 5 August 2024.
Winner Announcement
On behalf of the chairs of IECMA 2024, we are pleased to announce the winners of the Best Oral Presentation Award and Best Poster Award.
The Best Oral Presentation Awards have been awarded to:
-Sciforum-087723, Current Measurements for the characterization of SiC power devices used in electric traction drives. Maria Giorgia Spitaleri, Giuseppe Scarcella, Mario Cacciato and Giacomo Scelba.
-Sciforum-088658, Early fault diagnosis of rotor cage bars and stator windings of induction motor based on axial flux signal using transfer learning. Maciej Skowron
The Best Poster Awards have been awarded to:
-Sciforum-087677, Evaluation of Wire Arc Additive Manufacturing for Cavitation Erosion-Damaged Blade Repairs. Shinichiro Ejiri
-Sciforum-091074, Fault Diagnosis of the Hydraulic System for a Bridge Erecting Machine Based on Ontology Bayesian Networks.Huan Zhang and Gangfeng Wang.
Welcome from the Chair
Dear Colleagues,
It is our pleasure to invite you to join the 2nd International Electronic Conference on Machines and Applications (IECMA 2024) after the strong success of the previous annual online conference. IECMA 2024 will be held online from 18 to 20 June 2024.
Machinery and engineering areas play a key role in an ever-increasingly technological society. Transportation, renewable energies, and more efficient buildings are only some of the domains where the intensive application of these systems has been most noticed. In all these applications, efficiency and reliability, automation and control, and advanced manufacturing are of major concern.
The scope of this online conference is to bring together well-known worldwide experts who are currently working on machinery and engineering and to provide an online forum for presenting and discussing new results.
Throughout this event, we aim to cover, among others, the following topics:
S1. Additive Manufacturing
S2. Condition Monitoring and Fault Diagnosis
S3. Automation and Control Systems
S4. Mechatronic and Intelligent Machines
S5. Turbomachinery
S6. Electrical Machines and Drives
S7. Vehicle Dynamics and Control
All accepted abstracts will be published on the website of the conference. You are required to submit an abstract (minimum 200—maximum 300-word limit). Please see the abstract guidelines in "Instructions for Authors".
After the conference, the participants may submit a full paper to MDPI’s Machines journal. After the review process, the authors of the accepted papers will receive a 20% discount on the APC before the paper is published in Machines.
On behalf of the Organizing Committee, we cordially invite you to join us at the 2nd International Electronic Conference on Machines and Applications (IECMA 2024).
We look forward to your contributions.
Sincerely,
Prof. Dr. Antonio J. Marques Cardoso
Chair of the 2nd International Electronic Conference on Machines and Applications
Follow the conference organizer on Social Media
Event Chair

CISE – Electromechatronic Systems Research Centre, University of Beira Interior, Calçada Fonte do Lameiro, Covilhã, Portugal
Antonio J. Marques Cardoso received the Dipl. Eng., Dr. Eng., and Habilitation degrees from the University of Coimbra, Coimbra, Portugal, in 1985, 1995 and 2008, respectively, all in Electrical Engineering. From 1985 until 2011 he was with the University of Coimbra, Coimbra, Portugal, where he was Director of the Electrical Machines Laboratory. Since 2011 he has been with the University of Beira Interior (UBI), Covilhã, Portugal, where he is Full Professor at the Department of Electromechanical Engineering and Director of CISE - Electromechatronic Systems Research Centre (http://cise.ubi.pt). He was Vice-Rector of UBI (2013-2014). His current research interests are in fault diagnosis and fault tolerance in electrical machines, power electronics and drives. He is the author of a book entitled Fault Diagnosis in Three-Phase Induction Motors (Coimbra, Portugal: Coimbra Editora, 1991), (in Portuguese), editor of a book entitled Diagnosis and Fault Tolerance of Electrical Machines, Power Electronics and Drives (IET/SciTech, UK, 2018) and also author of around 600 papers published in technical journals and conference proceedings. Prof. Marques Cardoso currently serves as Editor-in-Chief of the MDPI journal Machines, Editor of the IEEE Transactions on Energy Conversion and IEEE Power Engineering Letters, and Associate Editor of the IEEE Transactions on Industry Applications, IEEE Transactions on Power Electronics, IEEE Journal of Emerging and Selected Topics in Power Electronics, IEEE Open Journal of the Industrial Electronics Society, IET The Journal of Engineering, as well of the Springer journal Electrical Engineering and the International Journal of Systems Assurance Engineering and Management.
Session Chairs

Prof. Dr. Jose Alfonso Antonino-Daviu
Department of Electrical Engineering, Universitat de València, Valencia, Spain
Electrical Machines and Drives

Dr. Daejong Kim
Department of Mechanical and Aerospace Engineering, The University of Texas at Arlington, Arlington, USA
Friction and Tribology

Prof. Dr. Kai Cheng
College of Engineering, Design and Physical Sciences, Brunel University London, London, UK
Additive Manufacturing

Prof. Dr. Hui Ma
School of Mechanical Engineering and Automation, Northeastern University, Shenyang, China
Condition Monitoring and Fault Diagnosis

Prof. Dr. Dan Zhang
Department of Mechanical Engineering, The Hong Kong Polytechnic University, Hong Kong, China
Automation and Control Systems

Dr. Matthias Meinke
Rheinisch-Westfälische Technische Hochschule Aachen, Aachen, Germany
Turbomachinery

Prof. Dr. Giuseppe Carbone
Department of Mechanical, Energy and Management Engineering, Università della Calabria, Rende, Italy
Mechatronic and Intelligent Machines

Dr. Yahui Liu
Driver-Vehicle Automation Collaboration & Shared Control Lab, School of Vehicle and Mobility, Tsinghua University, Beijing, China
Vehicle Dynamics and Control
Event Committee

DIMEG, Università della Calabria,Rende, Italy

School of Mechanical and Manufacturing Engineering, University of New South Wales, Sydney, Australia
mechanical engineering; design innovation; innovation and technology management; design history and theory; manufacturing engineering

Mechanical and Materials Engineering, School of Technology and Management, Instituto Politécnico de Viana do Castelo, Castelo, Portugal
dynamics; vibration and damping; smart materials and structures; computational and experimental mechanics; mechatronics and structural control; structural acoustics; impact and wave propagation; structural health monitoring; composite structures; machine

Department of Civil and Industrial Engineering—DICI, University of Pisa, Pisa, Italy
machine design; structural dynamics; fatigue and fracture; residual stresses; contact mechanics

Department of Mechanical Engineering, ISEP–School of Engineering, Polytechnic of Porto, Porto, Portugal
manufacturing processes; automation and robotic systems; material properties; microhardness; microstructures; hard coatings; wear; friction

Department of Electrical, Electronics and Computer Engineering, University of Catania, Catania, Italy
control algorithms for electric drives; fault-tolerant motor drives; electric traction; power electronic converters for electric mobility

LARM2: Laboratory of Robot Mechatronics, Department of Industrial Engineering, University of Rome Tor Vergata, Roma, Italy
mechanism design mechanics of robots; robot design

Engineering Department, University of Ferrara, Ferrara, Italy
kinematics; dynamics; mechanism and machine theory; parallel manipulators; robot mechanics; biomechanics; vehicle mechanics; robotics

Dipartimento di Ingegneria Civile e Ambientale, Politecnico di Milano, Milano, Italy
MEMS; smart materials; micromechanics; machine learning-driven materials modeling

Department of Mechanical Engineering, National University of Singapore, Singapore, Singapore
laser–materials interactions; laser-based advanced manufacturing; powder bed fusion; Additive manufacturing; 3d printing

Faculty of Engineering, University of New South Wales, Sydney, Australia
computational mechanics; non-deterministic modelling and methods; AI and machine learning in structural analysis and design; stochastic structural analysis and safety assessment in CAD/CAE; composite materials and structures

School of Computing, Mathematics and Engineering, Charles Sturt University, Bathurst, NSW, Australia
computational intelligence; bio-mechatronics systems; health technology and biomedical; vision-based cancer diagnosing; bio-signal/ image pattern recognition; artificial intelligent systems

Centre for Mechanical Technology and Automation, University of Aveiro, Aveiro, Portugal
manufacturing processes; welding, fracture mechanics; welding of composites; laser welding

Lane Department of Computer Science & Electrical Engineering, West Virginia University, Morgantown, WV, USA
finite element analysis; internal combustion engines; linear motors; pistons; stirling engines; alternators; distributed control; distributed sensors; equivalent circuits

advanced manufacturing systems; automation and robotics; industrial design

health condition monitoring and intelligent maintenance; big-data era intelligent diagnostics and prognostics; reliability evaluation and remaining useful life prediction; mechanical signal analysis and processing; mechanical system dynamic modeling

nonlinear dynamics; non-linear mechanics; control; biomechanics; mechatronics
dynamics; vibration; structural dynamic modification; dynamic model updating; experimental dynamic substructuring; friction induced vibrations

machine tools; machining; grinding; physics and chemistry of solids; advanced manufacturing

condition monitoring; plant maintenance

computational design; CAD/CAM/CAE; digital manufacturing; product design; FEA; industry 4.0; prototyping; reverse engineering

networked multi-agent system; network control system; aircraft control; wind power system control; anti-interference control

Industry 4.0; maintenance; production engineering; systems reliability; lean maintenance; decision support systems; artificial inteligence; machine learning

School of Mechanical Engineering, National Technical University of Athens, Greece
manufacturing technology; machining processes; non-conventional machining; modeling and simulation

Department of Mechanical and Electrical Engineering, School of Engineering, Ocean University of China, China
multiple degrees of freedom; active and semi-active vibration control; mechanical network; semi-active device design; vibration control of marine equipment; marine platforms; vehicles
Department of Mechanical Engineering, University of Saskatchewan, Canada
design; manufacturing; MEMS; dynamic systems; biorobotics; biosensors; bioacutators

Department of Mechanical Engineering, University of Maryland, USA
dynamics; vibration; control; structural health monitoring; renewable energy; metamaterials; infinitely variable transmission

Faculty of GeoEngineering Mining and Geology, Wrocław University of Science and Technology, Poland
mining machines; field measurements; condition monitoring; advanced signal processing; data analytics; acoustics; predictive maintenance

Electrical and Computer Engineering Department, Curtin University, Australia
condition monitoring; fault diagnosis; asset management; power electronics; power system stability quality and control; renewable energy; smart grids

Department of Mechanical and Industrial Engineering, University of Toronto, Canada
multidisciplinary engineering design; multiscale analysis and design of multifunctional lightweight structures
Department of Control Identification Diagnosis, University of Lorraine, France
identification, state estimation, and control of dynamical systems; cable-driven robot; actuators

wind engineering; wind energy; renewable energy technologies; wind turbines; wind; power systems analysis

Institute of Digitalization, IMC University of AppliedSciences Krems, Austria
software engineering; requirements engineering; software architecture; systems design-analysis and validation; adaptability and flexiblilty in systems design; configuration and re-configuration of systems; product line engineering; data-driven systems; bu

Department of Electrical and Computer Engineering, University of Coimbra, Portugal
electrical energy; electric machines; electric vehicles; electromechanical systems; energy efficiency; renewable energy; energy storage

Department of Innovation Engineering, University of Salento, Italy
mechatronics; automation; control of mechanical systems; design and testing of sensors systems

Department of Electrical Engineering, University of Málaga, Spain
multiphase electric drives; model predictive control; fault-tolerant control

mechanical design; robotics; synthesis of mechanism; parallel robots; medical robot; safety

School of Mathematics and Statistics, Shandong Normal University, China
impulsive control theory; hybrid systems; time-delay systems; neural networks and applied mathematics

Department of Mechanical Engineering, South Dakota State University, USA
multiscale modeling and simulation; process-structure-property-performance relations of materials; high strain rate performance of materials; mechanical and machine design; crashworthiness analysis

Department of Mechanical Engineering, College of Engineering, University of Alaska Anchorage, USA
flexure hinges and compliant mechanisms; system dynamics; dynamics and vibrations; system analogies; micro and nano electromechanical systems

Center for Micro-BioRobotics, Istituto Italiano di Tecnologia, Italy
model-based design; modeling/simulation; flexible tools; biomedical robotics; bioinspired robotics; soft robotics
Politecnico di Torino, Department of Mechanical and Aerospace Engineering, , Italy
servosystems; modeling and simulation; mechatronic systems; rotary and fixed wing actuation systems; prognostics and health management; test bench design and simulation

Department of Mechanical Engineering, Florida International University, Miami, USA
additive manufacturing; structural health monitoring; signal processing; system identification; artificial intelligence applications

School of Science, Engineering and Environment, University of Salford, UK
metamorphic/reconfigurable mechanisms and robotics; rehabilitation and prosthetics; smart mechanical transmission systems

nonlinear control; sliding mode control; robotics; hybrid systems; time-delay systems
Invited Speakers

Department of Civil and Industrial Engineering—DICI, University of Pisa, Pisa, Italy
Speech Title: Resonant test rig for rotating fatigue testing of drill pipes
Prof. Santus is full professor at the DICI department of the University of Pisa, Italy, and is involved in research of strength of materials and fatigue of metals. The topic presented here is about the description of atest rig for the rotating fatigue of drill pipes, based on resonance, and in particular thedetection and then the observation of the failure of the tested specimens.
S2. Condition Monitoring and Fault Diagnosis

Department of Engineering "Enzo Ferrari", University of Modena and Reggio Emilia, Italy
Speech Title:Wound field synchronous machines for propulsion: state of the art and trends
Stefano Nuzzo (S’17-M’18-SM’23) received his Ph.D. degree in Electrical and Electronic Engineering in 2018 from the University of Nottingham, Nottingham, U.K, where he worked also as a Research Fellow within the Power Electronics, Machines and Control (PEMC) Group. In January 2019, he moved to Modena, Italy, where he is currently a Tenure Track Assistant Professor in Electric Machines and Drives at the Department of Engineering “Enzo Ferrari” of the University of Modena and Reggio Emilia. His research interests are the analysis, modelling and optimization of electrical machines and drives, with focus on sustainability and reliability design approaches of synchronous drives based on radial flux machines for industrial and traction applications.
S6. Electrical Machines and Drives

Department of Electrical Electronic and Computer Engineering, University of Catania, Catania, Italy
Speech Title:Resolution of Rotor Position Measurement in Electric Drives: Modelling and Impact on Speed Estimation
Giacomo Scelba (Senior, IEEE) received the M.S. and Ph.D. degrees in electrical engineering from the University of Catania, Italy, in 2002 and 2006, respectively. He is currently an Associate Professor with the Department of Electrical Electronic and Computer Engineering (DIEEI), University of Catania, Italy. He has authored or coauthored more than 180 peer-reviewed and refereed technical publications and holds one U.S. patent. He is responsible of national and international research projects. He served on the organization of several IEEE conferences, including Topic Chair for ECCE in the years 2013-2024, Session Chair for IEEE EPE in the years 2019 and 2023 ECCE Europe and Vice Chair for ECCE 2022. Dr. Scelba currently serves as Secretary of the IEEE PELS Technical Committee on Electrical Machines, Drives and Automation. He is Member of the IES Electrical Machines Committee, the IAS Industrial Drives Committee, the IAS Electric Machines Committee, the IAS Industrial Power Converters Committee. Dr. Scelba received the 2014 First Prize Paper Award and the 2016 Third Prize Paper Award from the IAS Industrial Drives Committee, and the 2018 Third Prize Paper Award from the IES Electrical Machine Technical Committee. He was also honored with the 2021 Outstanding Reviewer Award from IEEE Power Electronics Society. Dr. Scelba currently serves as an Associate Editor for the IEEE JOURNAL OF EMERGING AND SELECTED TOPICS IN POWER ELECTRONICS and the IEEE TRANSACTIONS ON INDUSTRY APPLICATIONS. His recent research interests include ac drive control technologies, fault-tolerant motor drives, modeling and control of power converters, and advanced technologies for power electronics applications.
Session: S6. Electrical Machines and Drives

Speech Title:WBG based power converters for green transportation: challenges and design solutions;
Davide Barater received the Ph.D. degree in Information Technology in 2014 from the University of Parma Italy. He is currently Associate Professor at the University of Modena and Reggio Emilia, Italy. His research area is focused on power electronics and electrical machines for e-mobility and motor drives. He is the Coordinator of the European Project AUTO-MEA that aims to develop novel solutions for windings structures based on hairpin technology for improved power density, efficiency and increased frequency operation.
S6. Electrical Machines and Drives;

Speech Title: Dynamic Vision-Enabled Contactless Machine Micro-Vibration Sensing and Fault Diagnosis;
Xiang Li, Associate Professor at Xi'an Jiaotong University, China. He is an IET Fellow. His research interests include industrial AI, machine vision, neuromorphic computing, predictive maintenance, event camera, etc. Have published over 60 high-level research papers, including 21 ESI highly cited papers and 7 ESI hot papers. His citations on Google Scholar are over 8000 with H-index of 41. He was selected as Highly Cited Researcher by Clarivate, and top 2% scientists in career worldwide by Elsevier and Stanford University.
S2. Condition Monitoring and Fault Diagnosis;

Speech Title:A novel variable stiffness mechanism and its application in human-robot interaction
Prof. Shaoping Bai is a full professor at the Department of Materials and Production, Aalborg University (AAU), Denmark and the founder of AAU startup BioX ApS. His research interests include wearable sensors, medical and assistive robots, and exoskeletons. He leads several national and international research projects in exoskeletons, including EU AXO-SUIT and IFD Grand Solutions project EXO-AIDER, and Danish Independent Research Council project VIEXO, among others. He is a recipient of IEEE CIS-RAM 2017 Best Paper Award, IFToMM MEDER 2018 Best Application Paper Award, WearRAcon2018 Grand Prize of Innovation Challenges, and 2023 IFToMM MESROB Best Student Paper Award. Prof. Bai was an associate editor of ASME J. of Mechanisms and Robotics, now serves in the editorial board of Robotica and MDPI Machines.
S3. Automation and Control Systems

Speech Title: Robot design: application to medical robotics
Med Amine Laribi , is a Full Professor in the Fundamental and Applied Sciences Faculty of the University of Poitiers (UP), where he teaches robotics and mechanic. He has a Mechanical Engineer Degree (specialization on Mechanical Design) from École Nationale d'Ingénieurs de Monsatir (E.N.I.M.) in 2001. M.S. in Mechanical Design, 2002. He received his Ph.D. in Mechanics from University of Poitiers in 2005 and National Habilitation in Mechanics from University of Poitiers in 2018. He servers as Associate Editor in several reputed internationals journals including ASME Journal of Medical Devices, Assembly Automation (Emerald Publishing), Mechanical Sciences (Copernicus Publications), MDPI Robotics. He is a member of international scientific committee of RAAD and MESROB. His research interests, at the Department of G.M.S.C. of Pprime Institute, include aspects on robots design, mechanism synthesis, cable driven robots, parallel robots, haptic interfaces, collaborative robots with more than 79 published peer reviewed journal papers, 11 edited books, 12 edited journal special issue, 7 PhD students. He is leading several national and international research projects in the fields of medical robotics and biomimetics. IFToMM Executive Council Member (2024-2027) and Chair of IFToMM TC Biomechanical Engineering.
S4. Mechatronic and Intelligent Machines

Speech Title: Industrial Challenges in the Vibration-based Condition Monitoring of Machines A brief introduction: With the advancements of technologies over decades, there are many publications on the topic of the Vibration-based Condition Monitoring. However, it seems that there is lack of synergy between the research and industrial requirements. The current limitations and the industrial challenges will be discussed during the lecture.
Prof. Sinha is internationally well-known experts inVibration-based Condition Monitoring and Maintenance of Machines and Structures. He is involved in and solved a number of industrial vibration problems of machines, piping and structures byin-situ vibration measurements and analysis in many plants in last 35 years. He is the author of more than 275 publications (Journals, conferences, books, edited book/conference proceedings and technical reports) and gave a number of keynote/invited lectures. He is author of two well-received books “Vibration Analysis, Instruments and Signal Processing” and “Industrial Approaches in Vibration-based Condition Monitoring” He is also co-author of two books. Prof. Sinha has started a series of anInternational Conference of Maintenance Engineering (IncoME) from August 2016. Prof. Sinha is theEditor-in-Chief, Journal of Maintenance, Reliability and Condition Monitoring (MARC),the Associate Editor of 4 international journals, and theEditorial Board Member of 4 international journals. Prof. Sinha is also technical committee member of IFTOMM Rotordynamics and several international conferences.
S2. Condition Monitoring and Fault Diagnosis

Department of Mechanical Engineering, University of Maryland, Baltimore, USA
Speech Title: A Novel All-Geared Infinitely Variable Transmission for Tidal Energy Harvesting
Weidong Zhu is a Professor in the Department of Mechanical Engineering at the University of Maryland, Baltimore County, and the founding director of its Dynamic Systems and Vibrations Laboratory and Laser Vibrometry and Optical Measurement Laboratory. He received his double major BS degree in Mechanical Engineering and Computational Science from Shanghai Jiao Tong University in 1986, and his MS and PhD degrees in Mechanical Engineering from Arizona State University and the University of California at Berkeley in 1988 and 1994, respectively. He is a recipient of the 2004 National Science Foundation CAREER Award. He has been an ASME Fellow since 2010, and has served as an Associate Editor of the ASME Journal of Vibration and Acoustics and the ASME Journal of Dynamic Systems, Measurement, and Control, as a Subject Editor of the Journal of Sound and Vibration, and as a Topical Associate Editor of Nonlinear Dynamics. His research spans the fields of dynamics, vibration, control, structural health monitoring, renewable energy, and metamaterials, and involves analytical development, numerical simulation, experimental validation, and industrial application. He has published 328 SCI-indexed journal papers in these areas and has ten issued U.S. patents. He is a recipient of the 2020 University System of Maryland Board of Regents Faculty Award for Excellence in Research and the 2024 ASME Rayleigh Lecture Award.
S7. Vehicle Dynamics and Control

Department of Product and Systems Design Engineering, University of Western Macedonia, 50100 Kila Kozani, Greece
Speech Title: Integrating AI into the shoe design process
Prof. Dr Panagiotis Kyratsis (www.kyratsis.com) is the Head of the Department of Product and Systems Design Engineering, University of Western Macedonia, Greece. He is the Director of the Institute of Traditional Architecture and Cultural Heritage, University Research Center “TEMENUS” and the Director of the Computational Design and Digital Fabrication Research Lab (CODE+). He has been involved in a number of industrial projects and he has a great deal of expertise in both the design and the manufacturing aspects of product development. His main research interests include manufacturing, machining, CAD/CAM/CAE systems, computational design & CAD-based applications, product design, reverse engineering and prototyping. He has published more than 20 books and more than 190 papers in Scientific Journals and International Conferences. He acts as member of the editorial board and reviewer to numerous scientific journals and holds 12 industrial designs and two patents registered within the Greek Patent Office.
S1. Additive Manufacturing

Associate Researcher with Universitat Politècnica de València, Spain
Speech Title: High-frequency phenomena in electrical machines and their potential utilization for fault diagnosis and condition monitoring
Jose E. Ruiz-Sarrio received the double M.Sc. degree in industrial engineering and electrical engineering from Universidad Politècnica de València, Valencia, Spain, and Politecnico di Milano, Milan, Italy, in 2018, and the Ph.D. degree from the Technical University of Cluj-Napoca, Cluj-Napoca, Romania, in 2022. He was involved in the H2020 MSCA research project INTERACT which included Siemens Industry Software NV, Leuven, Belgium, as an industrial partner in his Ph.D. track, where he was an Associate Researcher for two years. Since 2023, he has been an Associate Researcher with Universitat Politècnica de València. His research interests include high-frequency phenomena, fault diagnosis, and condition monitoring in electrical machines and drives. He was the recipient of the Jorma Luomi Award in ICEM2022.
S6. Electrical Machines and Drives
Program Overview
For details of each day's program, please click each day below .
18th June Morning | 18th June Afternoon |
Session 3. Automation and Control Systems Session 4. Mechatronic and Intelligent Machines |
Session 6. Electrical Machines and Drives |
19th June Morning | 19th June Afternoon |
Session 2. Condition Monitoring and Fault Diagnosis |
Session 1. Additive Manufacturing |
IECMA 2024 Program (DAY 1)
IECMA 2024
Session 3. Automation and Control Systems
Session 4. Mechatronic and Intelligent Machines
Date: 18th June 2024 (Tuesday)
Time: 9:00 (CEST, Basel) | 03:00 (EDT, New York) | 15:00 (CST Asia, Beijing)
Time in CEST | Speaker | Title |
09:00-09:10 | Prof. Dr. Antonio J. Marques Cardoso |
Welcome from the conference chair |
09:10-09:15 |
Dr. Qi Zou |
Welcome from the session host |
09:15-09:35 | Prof. Dr. Shaoping Bai Invited Speaker |
A novel variable stiffness mechanism and its application in human-robot interaction |
09:35-09:50 |
Raul Campilho |
Development of an orthogonal transfer system for the automated warehouse industry |
09:50-10:05 |
Nirojh T |
Brake Fluid Level Management |
10:05-10:10 | Prof. Dr. Giuseppe Carbone Session Chair of S4 |
Welcome from the conference chair |
10:10-10:30 | Dr. Med Amine Laribi Invited Speaker |
Robot design: application to medical robotics |
10:30-10:45 |
Fernando A. V. Figueiredo |
SCARAmouche: A 3D-Printed Low-Cost SCARA Robot |
10:45-11:00 | Nikolaos Tapoglou Selected Speaker |
A CAD-Driven Approach to Cutting Tool Geometry Design of Solid end mills |
Session 6. Electrical Machines and Drives
Date: 18th June 2024 (Tuesday)
Time: 15:00 (CEST, Basel) | 09:00 (EDT, New York) | 21:00 (CST Asia, Beijing)
Time in CEST | Speaker | Title |
15:00-15:10 |
Dr. Jose E Ruiz Sarrió |
Welcome from the session host |
15:10-15:30 |
High-frequency phenomena in electrical machines and their potential utilization for fault diagnosis and condition monitoring |
|
15:30-15:50 | Dr. Stefano Nuzzo Invited Speaker |
Wound field synchronous machines for propulsion: state of the art and trends |
15:50-16:10 |
Dr. Giacomo Scelba |
Resolution of Rotor Position Measurement in Electric Drives: Modelling and Impact on Speed Estimation |
16:10-16:30 | Dr. Davide Barater Invited Speaker |
WBG based power converters for green transportation: challenges and design solutions |
16:30-16:50 | Prof. Dr. Weidong Zhu Invited Speaker |
A Novel All-Geared Infinitely Variable Transmission for Tidal Energy Harvesting |
16:50-17:05 | Sam Niroshan Thayapararajah Selected Speaker |
Development of an air pressure-sensing unit for domestic applications |
17:05-17:20 |
Maria Giorgia Spitaleri |
Current Measurements for the characterization of SiC power devices used in electric traction drives |
IECMA 2024 Program (DAY 2)
IECMA 2024
Session 2. Condition Monitoring and Fault Diagnosis
Date: 19th June 2024 (Wednesday)
Time: 9:00 (CEST, Basel) | 03:00 (EDT, New York) | 15:00 (CST Asia, Beijing)
Time in CEST | Speaker | Title |
09:00-09:10 |
Prof. Dr. Hui Ma |
Welcome from the session chair |
09:10-09:30 | Prof. Dr. Ciro Santus Invited Speaker |
Resonant test rig for rotating fatigue testing of drill pipes |
09:30-09:50 | Dr. Xiang Li Invited Speaker |
Dynamic Vision-Enabled Contactless Machine Micro-Vibration Sensing and Fault Diagnosis |
09:50-10:10 | Prof. Dr. Jyoti Sinha Invited Speaker |
Industrial Challenges in the Vibration-based Condition Monitoring of Machines |
10:10-10:25 | Maciej Skowron Selected Speaker |
Early fault diagnosis of rotor cage bars and stator windings of induction motor based on axial flux signal using transfer learning |
10:25-10:40 | Bruno Albuquerque de Castro Selected Speaker |
Condition Monitoring Applied to Power Transformers using an Acoustic Emission Technique |
Session 1. Additive Manufacturing
Date: 19th June 2024 (Wednesday)
Time: 15:00 (CEST, Basel) | 09:00 (EDT, New York) | 21:00 (CST Asia, Beijing)
Time in CEST | Speaker | Title |
15:00-15:10 | Prof. Dr. Kai Cheng Session Chair of S1 |
Welcome from the session chair |
15:10-15:30 | Prof. Dr. Panagiotis Kyratsis Invited Speaker |
Integrating Artificial Intelligence into the shoe design process |
15:30-15:45 |
Anastasios Tzotzis |
Design of additively manufactured and modularized low-cost Unmanned Surface Vessels for safety purposes |
15:45-16:00 |
Vasiliki Ε. Alexopoulou Selected Speaker |
Correlation of printing speed with the printing accuracy of resolution holes of a custom-made high-speed fused filament fabrication (FFF) printer |
16:00-16:15 | Alice Todeschini Selected Speaker |
Learning the buckled geometry of 3D-printed stiffeners of pre-stretched soft membranes |
16:15-16:30 |
Alok Bihari Singh |
Transforming Healthcare: A Review of Additive Manufacturing Applications in the Healthcare Sector |
Abstract Book
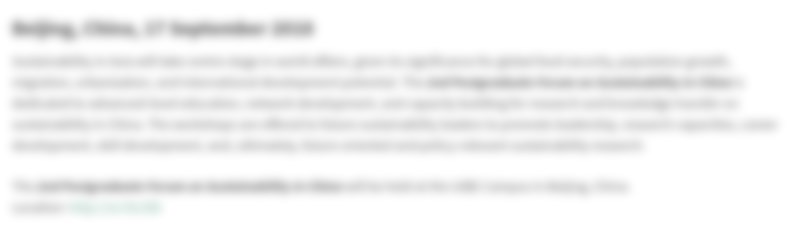
Live Session Recordings
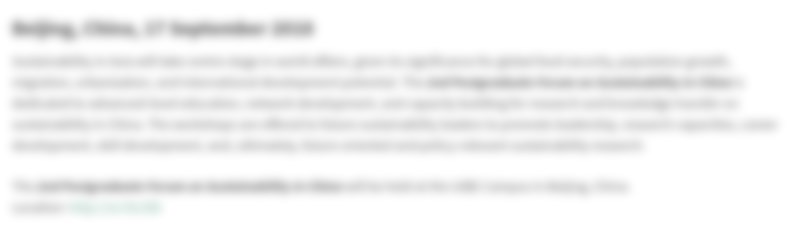
Registration
The registration for IECMA 2024 will be free of charge! The registration includes attendance to all conference sessions.
If you are registering several people under the same registration, please do not use the same email address for each person, but their individual university email addresses. Thank you for your understanding.
Please note that the submission and registration are two separate parts. Only scholars who registered can receive a link to access the conference live streaming. The deadline for registration is 13th June 2024 .
Instructions for Authors
Certificates of Participation are available in your logged-in area of Sciforum.net, under “My certificates” after the conference.
- The abstract structure should include the introduction, methods, results, and conclusions sections of about 200–300 words in length.
- All accepted abstracts will be published in the conference report of IECMA2024 in Engineering Proceedings (SCOPUS Indexed; ISSN: 2673-4591) after quality check. If you wish to publish an extended proceeding paper (4-8 pages), please submit it to the same journal after the conference.
- All abstracts should be submitted and presented in clear, publication-ready English with accurate grammar and spelling.
- You may submit multiple abstracts. However, only one abstract will be selected for oral presentation.
2. Please select only one presenter for each submission. If you would like to change the presenter after submission, please email us accordingly.
Note: We only accept live presentations.
b. File format: PDF (.pdf).
c. Size in cm: 60 width x 80 height–portrait orientation.
d. Font size: ≥20.
e. Maximum size: 250 M
You can use our free template to create your poster. The poster template can be downloaded here.
The Poster Sessions will take place in Zoom break-out rooms. The rooms will be called after your surname. You will automatically be assigned to your break-out room, however, you will be responsible for your own room, i.e. sharing your screen by yourself, handling the comments in the chat if there are any, etc. People will then be able to visit your room and discuss your poster with you. Please make sure you have the Zoom Desktop client or mobile app, version 5.3.0 or higher.
We will reach out to you closer to the dates of the conference with more information.
Publication Opportunities
- Machines Journal Publication
Participants in this conference are cordially invited to contribute a full manuscript to the conference's Special Issue, published in Machines (ISSN 2075-1702, Impact Factor 2.6), with a 20% discount on the publication fee. Details of the special issue will be announced here later. Please note that no other discounts are applicable. All submitted papers will undergo MDPI’s standard peer-review procedure. The abstracts should be cited and noted on the first page of the paper.
- Proceeding Paper Publication
You are welcome to submit a proceeding paper (4-8 pages) to Engineering Proceedings journal (ISSN: 2673-4591) after the conference.
Publication of the proceedings will be free of charge.
Authors are asked to disclose that it is a proceeding paper of the IECMA2024 conference paper in their cover letter.
Proceedings submission deadline: 5 August 2024
Carefully read the rules outlined in the 'Instructions for Authors' on the journal’s website and ensure that your submission adheres to these guidelines.
Manuscripts for the proceedings issue must be formatted as follows:-
Title.
-
Full author names.
-
Affiliations (including full postal address) and authors' e-mail addresses.
-
Abstract.
-
Keywords.
-
Introduction.
-
Methods.
-
Results and Discussion.
-
Conclusions.
-
Acknowledgements.
-
References.
-
List of accepted submissions (46)
Id | Title | Authors | |||||||||||||||||||||||||||||||||||||||
---|---|---|---|---|---|---|---|---|---|---|---|---|---|---|---|---|---|---|---|---|---|---|---|---|---|---|---|---|---|---|---|---|---|---|---|---|---|---|---|---|---|
sciforum-084434 | DEVELOPMENT AND EVALUATION OF BUILDING ENERGY EFFICIENCY THROUGH THE DESIGN AND IMPLEMENTATION OF AUTOMATION AND CONTROL SYSTEMS IN MOZAMBIQUE |
Show Abstract |
|||||||||||||||||||||||||||||||||||||||
The global push for sustainable development and lower energy usage has prompted increased interest in using automation and control systems in building infrastructures. These systems are now being investigated in Mozambique to determine their ability to increase energy efficiency. This study focuses on the complex processes of creating, deploying, and assessing these systems which use cutting-edge technology such as sensors, machine learning algorithms, and smart devices. The study includes case studies and experimental results that demonstrate the real-world usefulness of these methods. The capacity of automation and control systems to regulate temperature, lighting, and other energy-intensive components significantly reduces overall energy usage within buildings. Furthermore, these systems can discover and diagnose defects in a building's energy systems, allowing for fast and efficient repair—a critical factor in Mozambique, where energy supply is frequently unstable and maintenance is complex. The results of this study imply considerable energy savings, which will help to reduce the country's carbon footprint and advance sustainable development goals. The combination of advanced technologies, practical effectiveness in real-world scenarios, contextual relevance to Mozambique, a holistic approach, emphasis on timely maintenance, and the promotion of sustainable development make this study unique and valuable in building energy efficiency. In conclusion, this study catalyses the creation and implementation of Building Energy Management Systems in Mozambique by providing relevant insights for policymakers, building owners, and energy managers. |
|||||||||||||||||||||||||||||||||||||||||
sciforum-084879 | Innovations in FCHEV Power Management: A Fusion of Machine Learning and Physics-Based Models |
,
,
Guettaf Abderrazak ,
|
Show Abstract |
||||||||||||||||||||||||||||||||||||||
In the green motor vehicle era, fuel cell hydrogen electric vehicles (FCHEVs) are becoming promising alternatives. Thus, ensuring the proper operation of FCHEVs solely depends on advanced energy management systems (EMS). In this light, this work looks deeply into how combining machine learning and physics-based models can make FCHEVs operate effectively through improved EMSs. This study extensively analyzes how machine learning and physics-based models operate together in FCHEV-EMS. It therefore breaks through existing research and identifies insights, challenges, and potential future directions. It also looks closely at how machine learning meets challenges in adapting to real-time and handling changing conditions. To gain a better understanding of these issues, this study further recommends innovative ways to integrate machine learning flexibility within the precision of physics-based modeling. It therefore reveals an intriguing potential for additional study in the world of FCHEV-EMS. It represents the integration of machine learning and physics-based models as a potent technique to deal with EMS difficulties and accelerate advances in FCHEV energy management. In the end, it outlines significant findings, addressing why this integrated strategy is crucial in making FCHEVs a world-leading sustainable means of transportation. Through its comprehensive review and strategic perspectives, this initiative aims at catalyzing innovations that actively contribute to the sustainable advancement of FCHEVs. |
|||||||||||||||||||||||||||||||||||||||||
sciforum-084989 |
A driver-Assisted Automatic pneumatic braking system: conceptualized Product Development
, Delagamaathige Ravindu Deshaka Aluthwaththa ,
Ranamukage Wishwantha Wijayangana Ranamuka
Submitted: 06 Dec 2023 Abstract: Show Abstract |
,
Delagamaathige Ravindu Deshaka Aluthwaththa ,
Ranamukage Wishwantha Wijayangana Ranamuka
|
Show Abstract |
||||||||||||||||||||||||||||||||||||||
Driving is one of the prominent necessities of any individual. Due to the growth of the population, transportation has become tight, thus increasing the risk of accidents. There are several reasons that have been highlighted for such accidents, namely, long-distance driving without appropriate relaxation, driving at night, using mobile devices while driving, and driving under the influence of alcohol. Even though several pieces of research are available on automatic braking, this research specifically analyzes the importance of real-time data, while the system is driver-assisted. This research comprised an ultrasonic sensor, speed sensor, Arduino UNO Board, rain sensor, DC actuator, air compressor, and air reservoirs along with the major elements of the braking system. The results were analyzed in three various situations in wet and dry conditions. In addition, 1m of tolerance was provided for the internal adjustments of the vehicle. At first sight, if the distance between the object and the vehicle is larger than the braking distance tolerance limit, the system functions normally where activation is unnecessary. If the distance between the vehicle and the object interface is less than the braking distance tolerance limit, using the sensing mechanism, the brakes will be actuated and the vehicle will stop immediately. Finally, when the vehicle and object are too close, the system will not function again while giving a warning sign for the driver to steer in the proper direction. Overall, the variation in braking distance concerning vehicle speed was analyzed in both wet and dry conditions. Indeed, the research results provided a practically applicable automatic braking system with the driver’s control. This proactive method of accident mitigation represents a novel solution with the future scope of coordinating the automated braking system with a speed reduction system by regulating the accelerator's rotation. |
|||||||||||||||||||||||||||||||||||||||||
sciforum-085120 | Design of Disc Brake Dynamometer for Domestic Applications | , , |
Show Abstract |
||||||||||||||||||||||||||||||||||||||
Dynamometers are specifically designed for the measurement of the engine’s brake power. Although several types are physically available, disc brake dynamometers stand out as a more accurate and easily manipulable system. This paper aims to develop a highly accurate disc brake dynamometer while establishing the relationships between several process parameters. In the methodology, the initial stage was to measure the force requirements to the accelerator, brake lever, and clutch. A 3D model was developed using AutoCAD and the necessary accessories were identified. A CG125 engine was selected for the study. The most relevant preliminary design stages were formulated before the experimentation. An interface was added to display the outcome of the analysis. In the results, a real-time graphical relationship was built for brake power and engine speed. Seven sets of data in two different circumstances were obtained. The obtained results were validated against previous experimental results. Both sets of results were matched in most situations for the selected engine. The variation was comparatively less. The engine RPM was stipulated between 2000 and 8000, with the maximum power at the upper limit. The developed domestic application provided major benefits such as the control of the system at a single location, the automatic generation of relationships between the concerned parameters, the presence of a safety switch that can immediately halt the process in emergencies, the use of lambda sensors for corrections, and less maintenance. In terms of limitations, the system is limited to a permanent engine. Thus, this research can be further improved upon with the use of several engines at a time. Errors concerning the software can be avoided with comparative studies. Indeed, this dynamometer's precision and safety were improved more than any other type of conventional disc brake dynamometer. |
|||||||||||||||||||||||||||||||||||||||||
sciforum-086651 | Learning the buckled geometry of 3D-printed stiffeners of pre-stretched soft membranes | , , , , |
Show Abstract |
||||||||||||||||||||||||||||||||||||||
In this work, we propose an Artificial Intelligence (AI)-based methodology to learn the buckled configuration of stiffeners 3D-printed onto a pre-stretched soft membrane. The membrane acts as a muscle and, if properly pre-deformed, leads to the buckling of the stiffeners so that the resulting configuration can provide new system functionalities. Fused deposition modeling was carried out through a Voron 2.4 3D printer, specifically calibrated for PLA printing on a Lycra fabric. The printed PLA allows a controlled deformation of the substrate–stiffener system; different patterns or stiffeners geometries were investigated, to better understand their effects on the buckled configuration. A finite element model was then set to numerically reproduce the results obtained in the experimental campaign; to catch at best the outcomes, in terms of out-of-plane deflection in the buckled mode, an inverse problem was solved to tune the (nonlinear) constitutive models adopted for PLA and Lycra. Since the numerical model proved to be excessively time-consuming, a surrogate was developed by way of deep learning. In the first stage, YOLO (You Only Look Once) was used and trained properly for feature selection: different geometries of the stiffeners were allowed for and their classification was carried out, in addition to the numerical estimation of their relevant features related to the in-plane geometry. In the second stage, a regression part was added to the AI-based tool to learn the out-of-plane deflection, handled as a label in the learning stage. The results testify to the capability of the proposed approach and its efficiency for subsequent use in the shape optimization of the 3D-printed geometry to attain specific targets of coupled system response. |
Event Awards
To acknowledge the support of the conference's esteemed authors and recognize their outstanding scientific accomplishments, we are pleased to announce that the conference will provide 4 awards including the Best Oral Presentation Award and Best Poster Award.
The Awards
Number of Awards Available: 4
The Best Oral Presentation Award is given to the paper judged to make the most significant oral contribution to the conference.
The Best Poster Award is given to the submission judged to make the most significant and interesting poster for the conference.
There will be four winners selected for this award. The winner will receive a certificate and 200 CHF each.
Sponsors and Partners
For information regarding sponsorship and exhibition opportunities, please click here.
Organizers
Co-organizers
Media Partners
Conference Secretariat
Ms. Ariel Zhang
Ms. Charlene Dong
Email: iecma2024@mdpi.com
For inquiries regarding submissions and sponsorship opportunities, please feel free to contact us.
S1. Additive Manufacturing
Additive manufacturing (AM), also known as 3D printing, is a process of creating three-dimensional objects by depositing material, usually layer by layer, as opposed to traditional manufacturing methods such as machining and casting, which remove material to create the desired shape.
AM is a versatile and powerful technology that has the potential to revolutionize the way we manufacture products. It is already being used to create a wide range of products, from medical implants to aerospace components. As the technology continues to develop, we can expect to see even more innovative applications for AM in the future.
Session Chair
Prof. Dr. Kai Cheng, College of Engineering, Design and Physical Sciences, Brunel University London,UK
Show all published submissions (10) Hide published submissions (10)
Submissions
List of Papers (10) Toggle list
S2. Condition Monitoring and Fault Diagnosis
Condition monitoring and fault diagnosis is a kind of technology to understand and master the state of mechanical equipment in the use process, determine its overall or local normal or abnormal, early detection of faults and their causes, and can predict the development trend of faults, mainly including the identification of mechanical equipment condition and prediction of development trend.
Session Chair
Prof. Dr. Hui Ma, School of Mechanical Engineering and Automation, Northeastern University, China
Show all published submissions (13) Hide published submissions (13)
Submissions
List of Papers (13) Toggle list
S3. Automation and Control Systems
This session focuses on cutting-edge advancements in automated technologies, control strategies, and their applications across various industries. This session invites experts to share insights on robotics, AI-driven automation, sensor networks, cyber-physical systems, and innovative control methodologies, fostering discussions on enhancing efficiency, reliability, and performance in modern machinery and applications. It serves as a platform to explore the latest breakthroughs in automation technologies and control systems across diverse industries.
Session Chair
Prof. Dr. Dan Zhang, Department of Mechanical Engineering, The Hong Kong Polytechnic University, China
Show all published submissions (12) Hide published submissions (12)
Submissions
List of Papers (12) Toggle list
S4. Mechatronic and Intelligent Machines
This session delves into the dynamic domain of mechatronics, examining its pivotal role in shaping devices that enhance both human life and societal functions. From assistive tools designed for the elderly to automated solutions applicable in diverse sectors such as construction and farming, participants will explore the latest developments in product development, instrumentation, computer integration, and related areas. Attendees and contributors are invited to gain insights into mechatronic innovation, intelligent control, and the design of state-of-the-art intelligent machines.
Session Chair
Prof. Dr. Giuseppe Carbone, Department of Mechanical, Energy and Management Engineering, Università della Calabria, Italy
Show all published submissions (2) Hide published submissions (2)
Submissions
List of Papers (2) Toggle list
S5. Turbomachinery
Session Chair
Dr. Matthias Meinke, Rheinisch-Westfälische Technische Hochschule Aachen, Germany
Show all published submissions (1) Hide published submissions (1)
Submissions
List of Papers (1) Toggle list
S6. Electrical Machines and Drives
Electrical machines are energy conversion devices that play a crucial role in the development of nowadays societies. The research devoted to these devices is crucial for their improvement and optimization in order to adapt them to the new applications that rise in today societies. This section covers a wide range of aspects dealing with the design, optimization, control, monitoring and diagnostics of electrical machines. The considered applications include transportation electrification, grid-connected systems, energy production from renewables, energy harvesting, fault tolerant systems, and high-efficiency industrial conversion systems, among many others.
Session Chair
Prof. Dr. Jose Alfonso Antonino-Daviu, Department of Electrical Engineering, Universitat de València, Spain
Show all published submissions (5) Hide published submissions (5)
Submissions
List of Papers (5) Toggle list
S7. Vehicle Dynamics and Control
This session endeavors to investigate the most recent advancements in vehicle dynamics and control, encompassing a wide range of topics such as autonomous driving, human-machine co-driving, electric vertical take-off and landing (eVTOL) vehicles, artificial intelligence, control theory, dynamics analysis and modeling, system parameter identification and estimation, and simulation techniques. We welcome researchers to showcase their cutting-edge research, exchange insights on shaping the future of vehicles, and explore the interdisciplinary nature of vehicle dynamics and control to overcome challenges and drive advancements in this vital domain.
Session Chair
Dr. Yahui Liu, Driver-Vehicle Automation Collaboration & Shared Control Lab, School of Vehicle and Mobility, Tsinghua University, Beijing, China
Show all published submissions (3) Hide published submissions (3)
Submissions
List of Papers (3) Toggle list